How Alternators Work is an overview of the essential electrical machines that convert mechanical energy into alternating current (AC) electricity through the principle of electromagnetic induction. Alternators play a crucial role in various applications, most notably in automotive systems, where they are responsible for charging batteries and powering electrical components while the engine is running. As the demand for reliable electrical power sources has grown, the design and efficiency of alternators have evolved significantly, making them indispensable in both traditional and modern vehicles, including hybrids and electric cars.
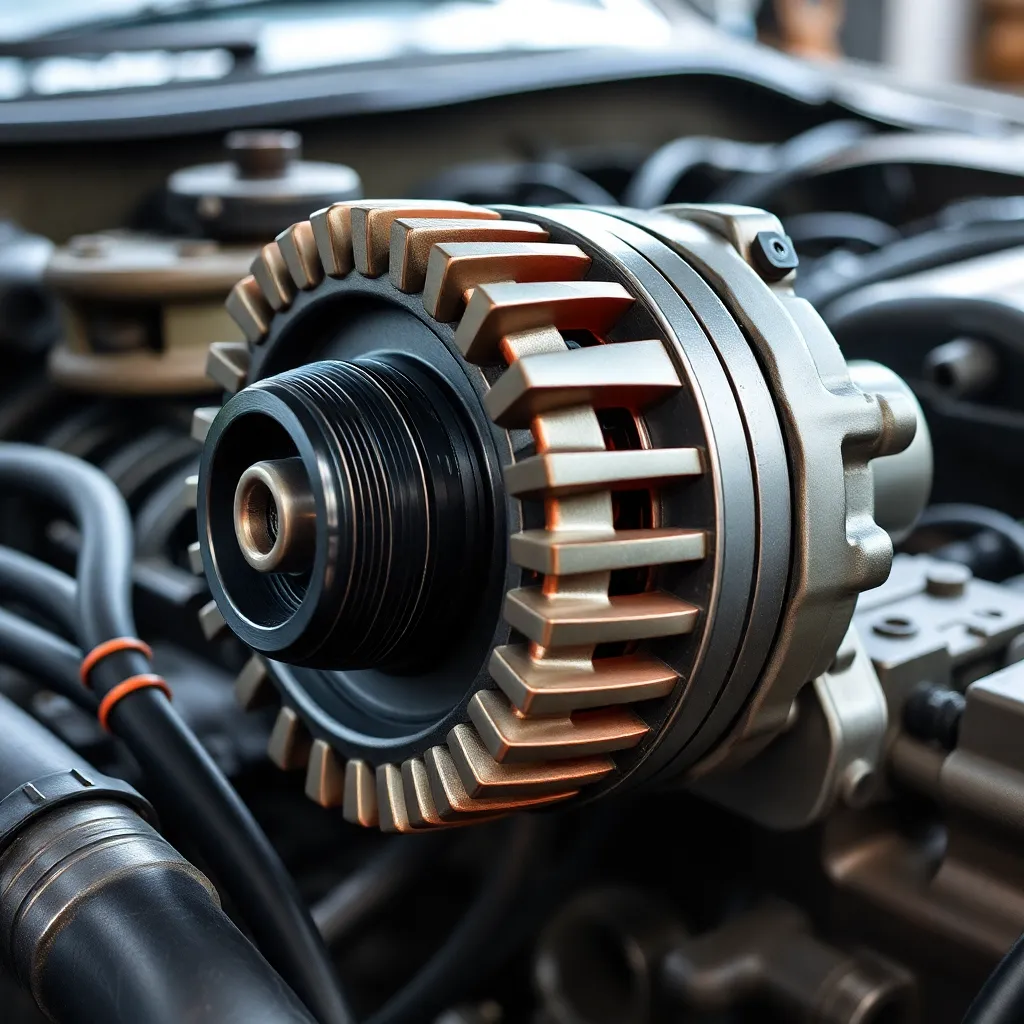
The history of alternators is rooted in the advancements of the Second Industrial Revolution, which saw the transition from steam and water power to electrical energy during the late 19th and early 20th centuries. Pioneers such as Thomas Edison and Nikola Tesla laid the groundwork for electrical generation, leading to the development of the first practical alternators in the 1870s. These innovations enabled more efficient power transmission over long distances, thus enhancing industrial productivity and transforming urban infrastructure.
By the early 20th century, mass production techniques further streamlined alternator manufacturing, embedding these devices into the fabric of modern electrical systems. Alternators operate based on electromagnetic induction, a principle articulated by Michael Faraday in the 1830s. They consist of key components such as the rotor, which generates a magnetic field, and the stator, where this magnetic field induces electromotive force (EMF) to produce AC electricity. Additional components like diode assemblies convert AC to direct current (DC) for practical use, and voltage regulators ensure consistent power output.
Different types of alternators, such as single-phase, three-phase, and automotive alternators, have emerged to meet varying demands, each with its specific design features and operational characteristics. Despite their critical function, alternators are not without controversy. Issues surrounding efficiency, maintenance, and the production of electromagnetic interference can pose challenges. Advanced designs, such as Permanent Magnet Alternators (PMAs), offer improved efficiency and reduced maintenance, but they come with higher initial costs.
As energy efficiency becomes increasingly important in automotive engineering, the ongoing development of alternators is essential to meet both performance expectations and environmental standards.
The development of alternators is closely tied to the broader technological advancements of the 19th and early 20th centuries, particularly during the Second Industrial Revolution. This period, extending from approximately 1865 to 1900, was marked by significant innovations that transformed the American way of life and had global implications. The introduction of electricity and advances in mechanical engineering played a crucial role in this transformation, which set the stage for the invention of the alternator.
Initially, industrialization relied heavily on steam power and water wheels, but the late 19th century saw a shift towards electrical power, particularly with the establishment of the modern electrical grid around the early 1880s. Pioneers like Thomas Edison and Nikola Tesla were instrumental in the race to electrify the world, with Edison’s work on electric lighting and Tesla’s contributions to alternating current (AC) systems laying the groundwork for the development of the alternator.
The first practical alternators were developed in the 1870s, during a time when electricity was beginning to be harnessed for more than just light. These early devices were crucial for generating AC electricity, which allowed for more efficient transmission over long distances compared to direct current (DC). The technological innovations of this era, particularly in the fields of electromagnetism and mechanical engineering, allowed for the creation of machines that could generate alternating currents effectively, thereby enhancing the productivity of factories and the efficiency of urban infrastructure.
By the turn of the 20th century, advancements in manufacturing processes, notably the rise of mass production techniques exemplified by Henry Ford’s assembly line, further accelerated the production of electrical machinery, including alternators. The integration of engineers into management roles across various industries also facilitated the growth and refinement of electrical technologies, including those used in alternators.
As electricity became a cornerstone of modern life, the alternator emerged as a vital component in a variety of applications, from automotive systems to power generation plants, significantly influencing how energy was produced and utilized. This evolution of the alternator not only reflects the rapid technological progress of the time but also illustrates the interconnectedness of industrial advancements that characterized this transformative period in history.
The operation of alternators is fundamentally based on the principle of electromagnetic induction, a phenomenon first discovered by Michael Faraday in 1831. This principle states that an electromotive force (EMF) is generated in a conductor when it is exposed to a changing magnetic field. In the context of an alternator, this is achieved through the relative motion between the rotor, which creates a magnetic field, and the stator, where the EMF is induced.
Key Components
Rotor
The rotor is the rotating component of the alternator. It is responsible for generating a magnetic field as it spins. This rotation is typically driven by an external mechanical source, such as an engine. The design of the rotor is critical, as it needs to ensure a strong magnetic field for effective induction.
Stator
The stator is the stationary part of the alternator, positioned around the rotor. When the rotor spins, the changing magnetic field it creates induces an electromotive force within the stator windings. This induced EMF is what ultimately results in the generation of alternating current (AC) electricity.
Diode Assembly and Voltage Regulator
Once the EMF is generated in the stator, it is typically in the form of alternating current. A diode assembly is employed to convert this AC into direct current (DC), making it suitable for charging batteries and powering electrical systems. Additionally, a voltage regulator is used to maintain a consistent voltage output, ensuring that the electrical systems operate effectively.
Electromagnetic Induction in Alternators
The core concept of electromagnetic induction in alternators relies on the interaction between the magnetic field and the electrical conductors within the stator. As the rotor turns, the magnetic field lines are cut by the stationary conductors, producing an induced electromotive force (induced EMF) across them. This process is not only essential for electricity generation in alternators but also underpins the operation of many other electrical devices, such as transformers and electric motors.
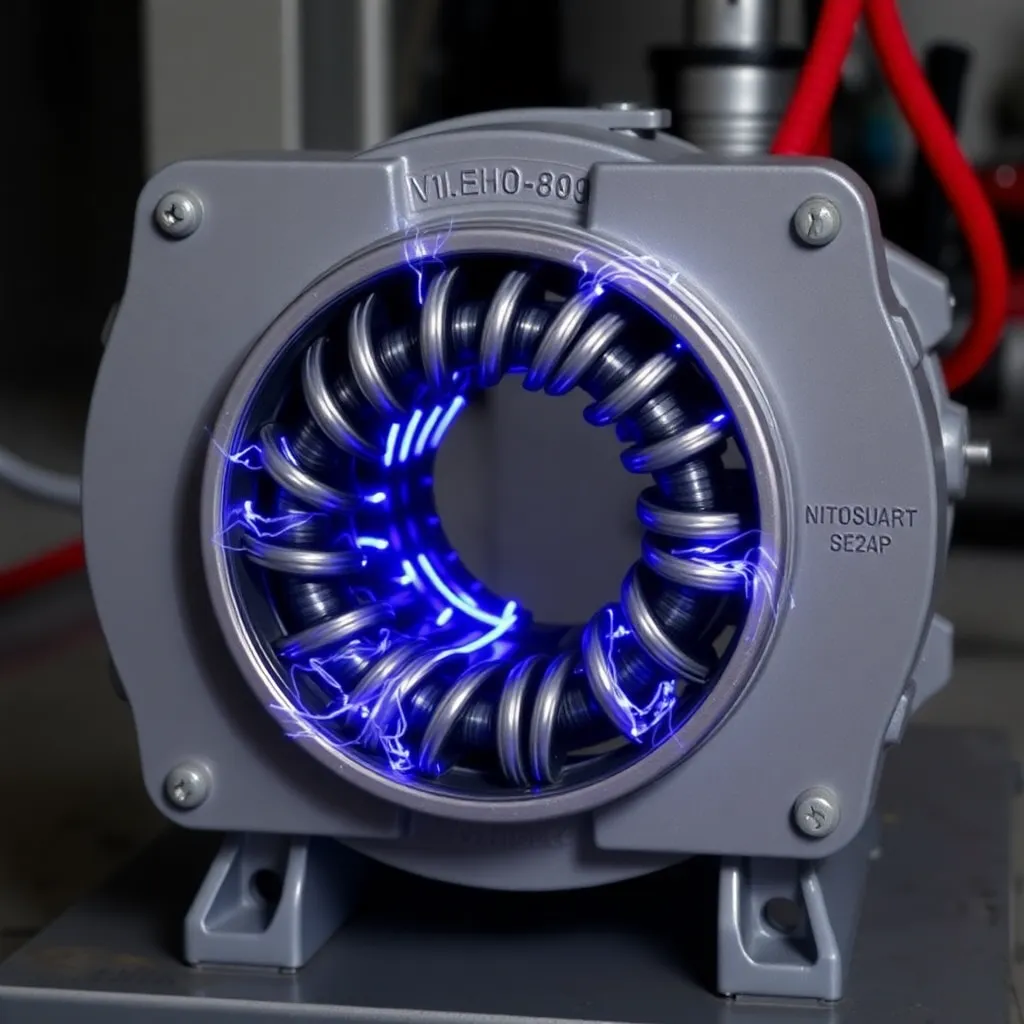
Alternators can be categorized based on their design and power output, with several common types being utilized across various applications.
Classification by Design
Alternators can be divided into two main types based on their design:
Salient Pole Rotor
Salient pole rotors are characterized by projecting poles that are used to generate a magnetic field. This design is often utilized in applications requiring a lower speed, such as hydroelectric power generation.
Smooth Cylindrical Rotor
Smooth cylindrical rotors have a uniform cylindrical shape and are commonly found in high-speed applications. They provide a consistent magnetic field and are typically used in large power plants.
Classification by Power Output
Alternators are also classified according to their output power capabilities, which include:
Single Phase Alternator
Single phase alternators generate one alternating voltage continuously. They are commonly used in small-scale applications, such as residential backup power systems.
Two-Phase Alternator
In a two-phase alternator, the winding generates maximum flux in one quarter of its cycle, while the second winding produces maximum flux in the next quarter. This type of alternator is less common but can be used in specialized applications.
Three Phase Alternator
Three-phase alternators are the most widely used type, generating three alternating voltages that are 120 degrees apart in phase. This configuration is particularly effective for industrial applications, as it provides a more stable power output and allows for the efficient distribution of electricity.
Other Types of Alternators
Beyond the basic classifications, alternators can also be designed for specific applications:
- Brushless Alternators: These alternators eliminate the need for brushes and slip rings, reducing maintenance requirements and wear. They are commonly used in large industrial and aviation applications.
- Automotive Alternators: Specifically designed for vehicles, these alternators convert mechanical energy from the engine into electrical energy to charge the battery and power the vehicle’s electrical systems.
- Marine and Diesel-Electric Alternators: These are tailored for use in boats and diesel locomotives, where robust performance and reliability are essential in demanding environments.
Automotive alternators are crucial components in modern vehicles, providing the necessary electrical power to support a wide range of applications. Their versatility is evident in various areas, including traditional internal combustion engine vehicles, hybrid electric vehicles (HEVs), and fully electric vehicles (EVs).
Automotive Systems
The primary function of alternators in automobiles is to charge the vehicle’s battery and power the electrical system while the engine is running. They convert mechanical energy from the engine into electrical energy, which is then used to operate essential components such as headlights, infotainment systems, and power windows. Modern vehicles often have sophisticated electrical systems that require consistent power supply and efficient voltage regulation, roles that contemporary alternators fulfill effectively.
Hybrid and Electric Vehicle Integration
With the increasing prevalence of hybrid and electric vehicles, the role of alternators has evolved significantly. In HEVs, alternators must handle higher voltage systems and support regenerative braking, which captures energy during deceleration and converts it back into electrical energy. This innovation enhances fuel efficiency and reduces emissions, making HEVs more environmentally friendly compared to traditional vehicles. Furthermore, in fully electric vehicles, while conventional alternators may be less common, the principles of energy conversion still apply in various forms of energy management systems.
Energy Efficiency Innovations
The push for energy-efficient solutions in the automotive industry has driven manufacturers to develop high-performance alternators that can meet the growing electrical demands of modern vehicles. Innovations include the use of lightweight materials and smart alternators that optimize energy use by adjusting output based on demand, further contributing to overall fuel economy and emission reductions. This trend reflects a broader commitment within the automotive sector to enhance vehicle performance while minimizing environmental impact.
Supporting Advanced Features
Alternators also play a vital role in supporting advanced features found in contemporary vehicles, such as driver-assistance technologies, infotainment systems, and connectivity modules. These systems require stable power supplies, which modern alternators are designed to provide reliably. Additionally, the integration of electric power steering and climate control systems adds to the electrical load that alternators must manage, emphasizing their importance in the vehicle’s electrical architecture.
Integration of Alternators in Power Systems
The performance management of alternators is critical to ensuring their efficiency and reliability within electrical systems. Alternators are essential components that convert mechanical energy into electrical energy, playing a vital role in various applications, from automotive systems to industrial power generation. Proper integration of alternators into power systems involves understanding their operational characteristics and implementing strategies that optimize their performance while minimizing costs and mechanical limitations.
Key Performance Indicators
To effectively manage the performance of alternators, several key performance indicators (KPIs) should be monitored. These include output voltage stability, current capacity, thermal efficiency, and operational lifespan. By regularly assessing these KPIs, technicians can identify potential issues and implement corrective actions before they lead to failures.
Optimization Techniques
Various optimization techniques can enhance the performance of alternators. For instance, strategies such as the Equivalent Consumption Minimization Strategy (ECMS) and Model Predictive Control (MPC) can be applied to manage power distribution effectively and improve energy efficiency in automotive applications. These methods allow for real-time adjustments based on driving conditions, thereby maximizing the alternator’s output while minimizing fuel consumption. Furthermore, employing advanced materials and designs can lead to significant performance improvements by reducing weight and enhancing power generation capacity.
Addressing Saturation Issues
One common challenge in alternator performance is saturation, which can limit output and lead to inefficiencies. To mitigate saturation issues, engineers may implement redesigns that adjust the motor’s functionality or upgrade the system components. Such modifications can enhance the overall performance of the alternator, allowing it to operate effectively under varying load conditions without compromising stability.
Regular Maintenance and Testing
Routine maintenance and testing are essential to maintaining the integrity of alternators in any power system. Electrical load testing, for instance, evaluates the alternator’s capacity to handle loads effectively, ensuring that it can meet the demands of the system. This proactive approach helps in identifying potential weaknesses and extending the lifespan of the alternator, ultimately leading to improved performance and reliability in the overall electrical system.
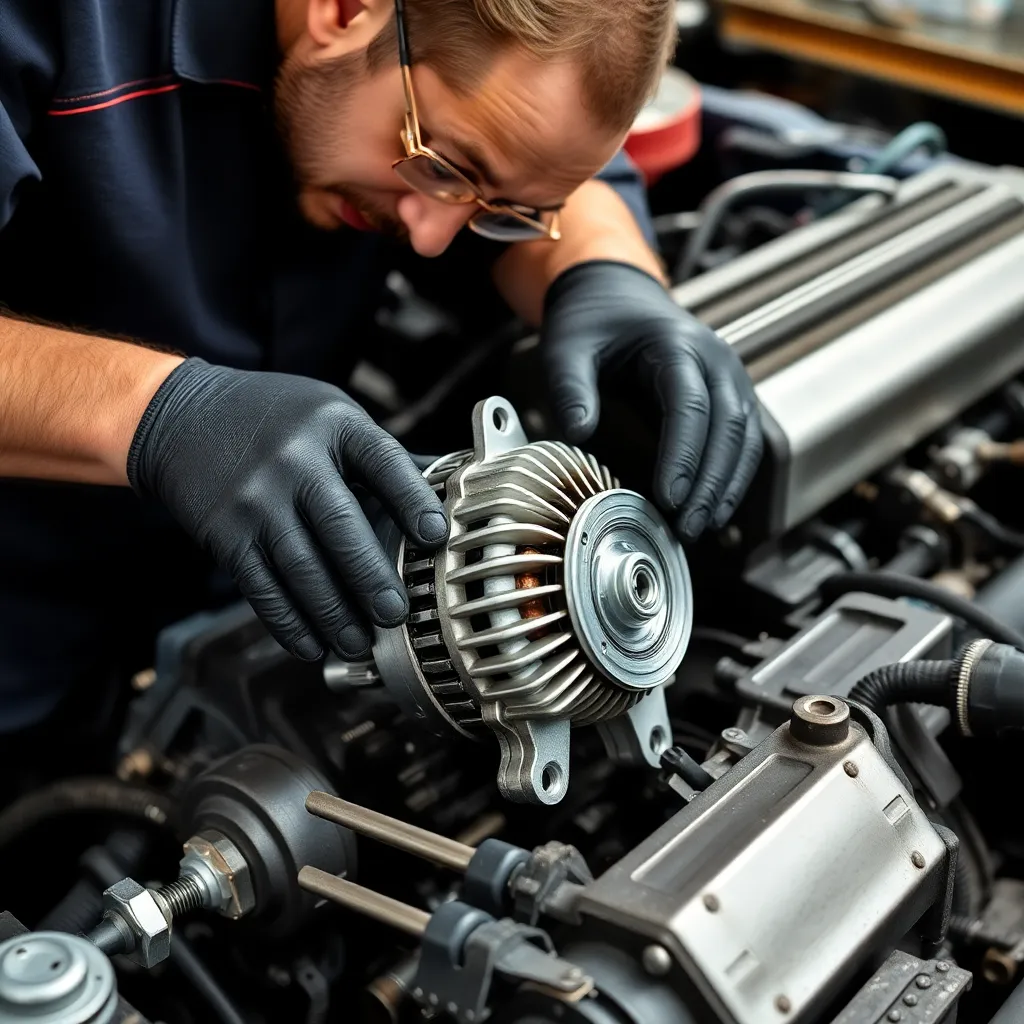
Advantages of Alternator
Alternators, particularly Permanent Magnet Alternators (PMAs), exhibit several advantages over traditional alternators. One of the most notable benefits is their higher efficiency ratings. PMAs can achieve efficiencies between 65-70%, significantly surpassing the typical efficiency of regular alternators, which ranges from 54 to 60%. This increase in efficiency can result in substantial fuel cost savings, with high-efficiency alternators saving upwards of 20% on fuel compared to their standard counterparts. Another advantage of PMAs is their durability and longevity.
These alternators are designed with fewer moving parts and lower maintenance requirements, which contributes to their overall reliability and ease of repair. This robustness makes PMAs particularly attractive for applications that demand sustainable and dependable power generation solutions. Additionally, the design of high-efficiency alternators, such as those employing NdFeB permanent magnets, minimizes excitation losses and reduces iron and stray losses, further enhancing their operational performance. This allows them to maintain high efficiency across a wider load range, improving grid utilization and reducing line losses.
Disadvantages of Alternator
Despite their advantages, alternators also come with certain disadvantages that must be considered. For instance, while PMAs may offer efficiency gains and reduced maintenance requirements, they typically have higher upfront costs compared to traditional alternators. This initial investment can be a barrier for some applications, particularly those with tighter budgets. Regular alternators, while less efficient, can provide cost-effective solutions in terms of initial purchase price and operational maintenance.
However, they may require more frequent maintenance, and improper care can lead to significant failures, accounting for up to 30% of alternator failures in vehicles. Moreover, alternators can produce electromagnetic interference (EMI) that may disrupt other electrical systems within a vehicle or machinery, necessitating additional shielding. This aspect is critical to consider, especially in applications where precision electronic systems are involved.
Can you explain the basic principles of electromagnetic induction that allow alternator to generate electricity?
The basic principles of electromagnetic induction that enable alternators to generate electricity are rooted in the concept discovered by Michael Faraday in 1831, known as Faraday’s law of induction. This law states that an electromotive force (emf) is induced in a conductor when the magnetic flux linking that conductor changes. An alternator is an electrical generator that converts mechanical energy into electrical energy in the form of alternating current (AC). It operates on the principle of electromagnetic induction, which means that when the magnetic flux through a conductor changes, an emf is induced in the conductor.
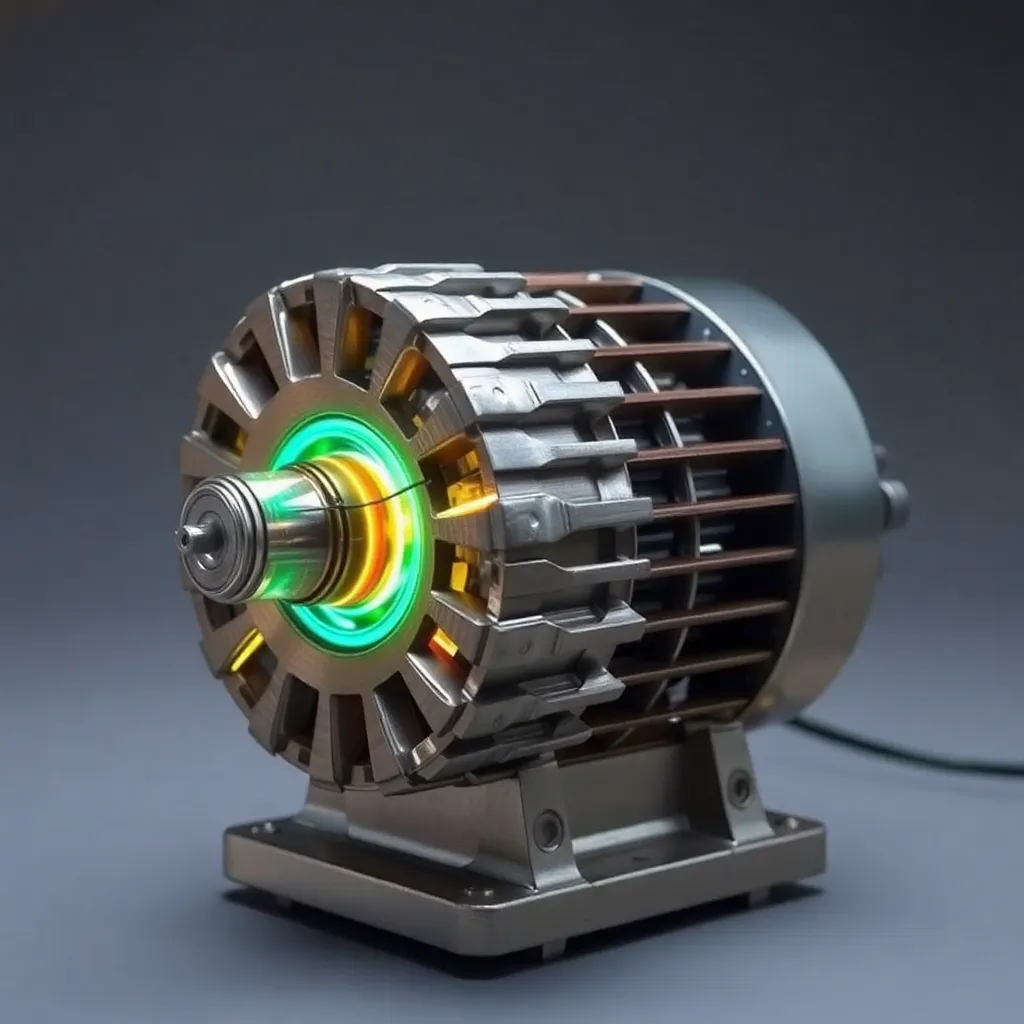
This principle is applied in both DC generators and alternators, though there are key differences in their construction and operation. Most alternators use a rotating magnetic field with a stationary armature to produce electricity. When the engine or another mechanical source turns the alternator’s rotor (which is essentially the rotating magnetic field), it causes a change in the magnetic flux through the stator (the stationary armature). This changing magnetic field induces an alternating current in the stator windings. In vehicles, for instance, the engine drives a belt that rotates a pulley attached to the alternator, causing the rotor to spin and generate electricity to charge the vehicle’s battery and power its electrical systems.
The induced AC current is typically converted to direct current (DC) by a rectifier within the alternator to be compatible with the vehicle’s electrical requirements. In power plants, larger three-phase alternators are used to generate the bulk of the world’s electrical power. These alternators are often driven by steam turbines and are known as turbo-alternators. These large machines function on the same basic principle of electromagnetic induction but on a much larger scale, providing the AC power that is distributed through electric power grids. In summary, the key principle behind how alternators work is electromagnetic induction, where mechanical energy is used to create a changing magnetic field, which in turn induces an electric current in a conductor
What are the main components of an alternator, and what roles do they play in the generation of electricity?
An alternator is an essential component in a vehicle’s electrical system, functioning as a generator that converts mechanical energy into electrical energy in the form of alternating current (AC). The main components of an alternator and their roles in the generation of electricity are as follows:
1. Rotor and Stator: The rotor and stator work together to generate electricity. The rotor is a rotating component that produces a magnetic field, while the stator is a stationary component that consists of a set of wire coils. As the rotor spins inside the stator, it induces a flow of alternating current in the stator windings.
2. Drive Pulley: The drive pulley is attached to the rotor shaft at the front of the alternator. The engine’s crankshaft turns the drive belt, which in turn spins the pulley on the rotor shaft, converting the mechanical energy from the engine into rotational energy required for generating electricity.
3. Rectifier: Although alternators generate AC power, most vehicle electrical systems require direct current (DC). The rectifier converts the AC output from the stator into DC power that can be used by the vehicle’s electrical components and to charge the battery.
4. Voltage Regulator: The voltage regulator maintains a consistent output voltage from the alternator to the vehicle’s electrical system, ensuring that the battery and electrical components receive the correct voltage to operate efficiently and safely.
5. Cooling System: Alternators generate significant heat during operation, and effective cooling is critical. Typically, alternators have vents on both the front and back to aid in heat dissipation. Some alternators may also have internal fans to improve airflow and cooling.
6. Housing: The alternator’s housing is usually made of aluminum, which is lightweight and does not magnetize. Aluminum also helps dissipate heat generated during the alternator’s operation. Understanding these components and their roles is fundamental to comprehending how alternators work to convert mechanical energy from the engine into electrical energy, which is vital for running a vehicle’s electrical systems and charging its battery.
Can you describe the different types of alternators and how their construction varies, particularly in terms of rotor and stator design?
Types of Alternators
1. Rotating Magnetic Field Alternator: This is the most common type of alternator used today. It features a stationary armature (stator) and a rotating magnetic field (rotor). This design is cost-effective and efficient for generating electrical power. The stator consists of iron cores and armature windings, while the rotor is typically made up of electromagnetic poles.
2. Linear Alternator: Unlike the traditional rotating magnetic field alternator, a linear alternator has a stationary magnetic field and a rotating armature. This type is less common and is used in specific applications where the traditional rotating design is not feasible.
3. Single-Phase and Three-Phase Alternator: Alternators can be designed to produce single-phase or three-phase AC output. Single-phase alternators are generally used in lower power applications, whereas three-phase alternators are used in industrial and large-scale power generation due to their efficiency and ability to deliver higher power.
Construction Differences
Stator Design
The stator is the stationary part of the alternator. It consists of: – Iron Core: Provides a low reluctance path for magnetic flux. – Armature Windings: These windings are where the voltage is induced by the rotating magnetic field of the rotor. In three-phase alternators, the windings are arranged to create three distinct but interconnected circuits, each generating an AC voltage.
Rotor Design
The rotor is the rotating part of the alternator. There are several types of rotors used in alternators, each serving different applications: – Salient Pole Rotor: Used in low-speed alternators, usually in hydroelectric power plants. The poles are large and protruding (salient) from the rotor body. They have a large diameter and short axial length. – Cylindrical Rotor: Also known as non-salient pole rotors, these are used in high-speed alternators, commonly found in thermal and nuclear power plants. They have a smooth cylindrical surface with slots cut out for the field windings.
What are the specific applications of each type of alternator, and what advantages do they offer in those contexts?
Alternators are versatile electrical generators that find applications in a variety of contexts, each benefiting from specific types of alternators tailored to the unique needs of those applications. Here, we will explore the different types of alternators, their applications, and the advantages they offer in those contexts.
1. Automotive Alternator: Automotive alternators are predominantly used in cars, trucks, and other vehicles. Their primary function is to convert mechanical energy from the engine into electrical energy, which charges the battery and powers the vehicle’s electrical systems, including lights, audio systems, navigation equipment, and heating systems. One of the key advantages of automotive alternators is their ability to provide a continuous and reliable source of electrical power while the vehicle is in operation, ensuring that all electrical components function optimally.
2. Industrial Alternator: Industrial alternators are used to power heavy machinery and equipment in factories and manufacturing plants. These alternators are designed to handle high power demands and are often larger and more robust than those used in automotive applications. The primary advantage of industrial alternators is their ability to sustain continuous operation under heavy loads, providing a stable and reliable power supply for critical industrial processes.
3. Residential Alternator: In residential settings, alternators are used in backup power generators. These generators provide electricity during power outages, ensuring that essential household appliances, such as refrigerators, lighting, and medical equipment, remain operational. The advantage of residential alternators is their ability to quickly respond to power outages and provide a seamless transition to backup power, minimizing disruption to daily life.
4. Permanent Magnet Alternator: Permanent magnet alternators are used in renewable energy systems, such as wind turbines and small hydroelectric generators. These alternators use permanent magnets to generate a magnetic field, which eliminates the need for a separate field excitation system. The primary advantage of permanent magnet alternators is their high efficiency and reliability, making them ideal for generating clean, renewable energy.
5. Marine Alternator: Marine alternators are specifically designed for use in boats and ships. These alternators are built to withstand harsh marine environments, including exposure to saltwater, humidity, and temperature fluctuations. The advantage of marine alternators is their durability and corrosion resistance, ensuring reliable performance in challenging conditions.
How do automotive alternator manage the varying electrical loads from different vehicle systems, and what impact does this have on performance?
Automotive alternators manage varying electrical loads from different vehicle systems by leveraging a combination of optimization techniques and advanced electronic control systems. The alternator’s primary function is to convert mechanical energy from the engine into electrical energy through a process of electromagnetic induction, which occurs within the stationary stator and rotating rotor assembly. This electrical energy is then rectified to direct current, which powers the vehicle’s electrical systems and charges the battery. To handle the fluctuating demands of modern vehicles, alternators employ various optimization methods and control strategies.
These include approaches such as Pontryagin’s Minimum Principle (PMP), Optimal Power Distribution (OPD), Equivalent Consumption Minimization Strategy (ECMS), and Model Predictive Controller (MPC). These techniques ensure that the alternator operates efficiently under different conditions by dynamically adjusting power output based on real-time requirements. Moreover, advanced algorithms like Driving Cycle Recognition (DCR) and Electrical Load Perception (ELP) help in identifying the vehicle’s operational state and adjusting the alternator’s output accordingly.
Real-Time Energy Management Strategies (R-EMS) further refine this process by continuously optimizing the distribution of electrical power within the vehicle. The impact of these varying electrical loads on vehicle performance is significant. When the alternator is unable to meet the required electrical load, the battery temporarily supplies the additional power needed. This ensures seamless functionality of essential and non-essential systems, from headlights to intricate onboard electronics, which is crucial for the vehicle’s optimal performance and safety.
However, any inefficiency in this balance can result in the engine expending more mechanical power to drive the alternator, potentially impacting fuel economy. Furthermore, electrical load testing is an important diagnostic process that evaluates the performance of a vehicle’s electrical system under simulated conditions. This helps in identifying potential issues within the alternator and other electrical components, preventing unforeseen breakdowns and enhancing vehicle longevity.
In summary, the management of varying electrical loads by automotive alternators involves a sophisticated interplay of electromagnetic processes, real-time optimization techniques, and strategic power distribution. This not only ensures the efficiency and reliability of the vehicle’s electrical systems but also supports overall vehicle performance and longevity.