In manufacturing industry there are several machining operations which are performed on metal stock but, out of all these operations 20% are hole making. Machine parts require holes for several purposes.
In general, we see seven types of holes in manufacturing.
- Through hole
- Blind hole
- Counter bore
- Blind hole with flat bottom
- Counter sink
- Spot facing
- Step drill

Types of holes
Following are the different operations performed on these holes.
- Drilling
- Boring
- Tapping
- Reaming
- Counter boring
- Countersinking
Among all six operations discussed above, only drilling is used for making hole. All the other processes are either used to increase the size of hole or to improve its quality.
Drill
Drill (or twist drill) is the cutting tool used for making holes in solid materials. It consists two parts: the shank which is used for holding purpose and the body consisting of cutting edges.
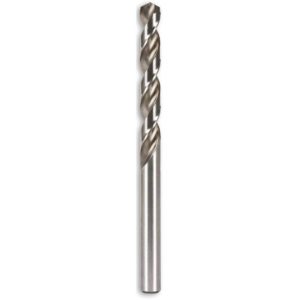
Twist Drill
Types of drill
Following are six types are drills which are mainly used in drilling operations.
-
Carbide tipped drills
For machining hard material in high volumes tungsten carbide coated drills are used.
-
Shell core drills
Shell core drills are for enlarging holes of larger diameter.
-
Spade drills
Spade drills are used to make small diameter holes with low cutting speeds and high feed rates.
-
Core drills
Core drills are used for enlarging already existing holes.
-
Oil hole drill
Oil hole drills are provided with internal holes extending to the length of drill. These holes are used to pump cutting fluid to the cutting edge.
-
Step drill
Step drills are used for counter boring, counter-sinking and multiple hole drilling.
Boring
Boring is the process of enlarging an already existing hole. Generally, a single point cutting tool is used for this operation.
Tapping
Tapping is the process of making internal threads in an already existing hole. A tap is a tool which is used for tapping.
Trepanning
Trepanning is the process of directly cutting circumference of the hole. At the end of trepanning, we are left with hole of required diameter and a core (metal stock).
Reaming
Reaming is done by a multitooth cutter which rotates and moves in an already existing hole. Reaming provides us smooth surfaces and close tolerances on the diameter of hole.
Image source:
Trepanning: https://edurev.in/question/2485477/Trepanning-operation-is-performed-fora-finishing-a
Types of holes: Manufacturing Technology, Volume 2, Third Edition, P N Rao