A bearing is a machine element that supports another moving machine element known as a journal. It enables a relative motion between the contact surfaces of the members while carrying the load. While doing so a certain amount of power is wasted in overcoming frictional resistance due to the relative motion between the contact surfaces. We need to study the types of Bearings, design, and materials used for bearings briefly. In the previous article, we discussed the different types of Bearings. Hydrodynamic Lubricated Bearings are a type of bearing that comes under Sliding Contact Bearings. In this article, let us discuss the Coefficient of Friction for Journal Bearings.
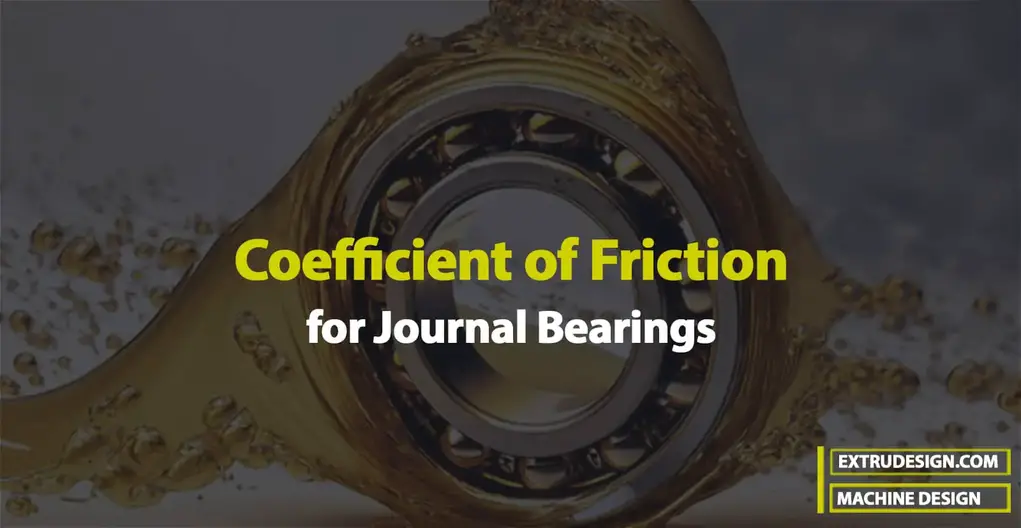
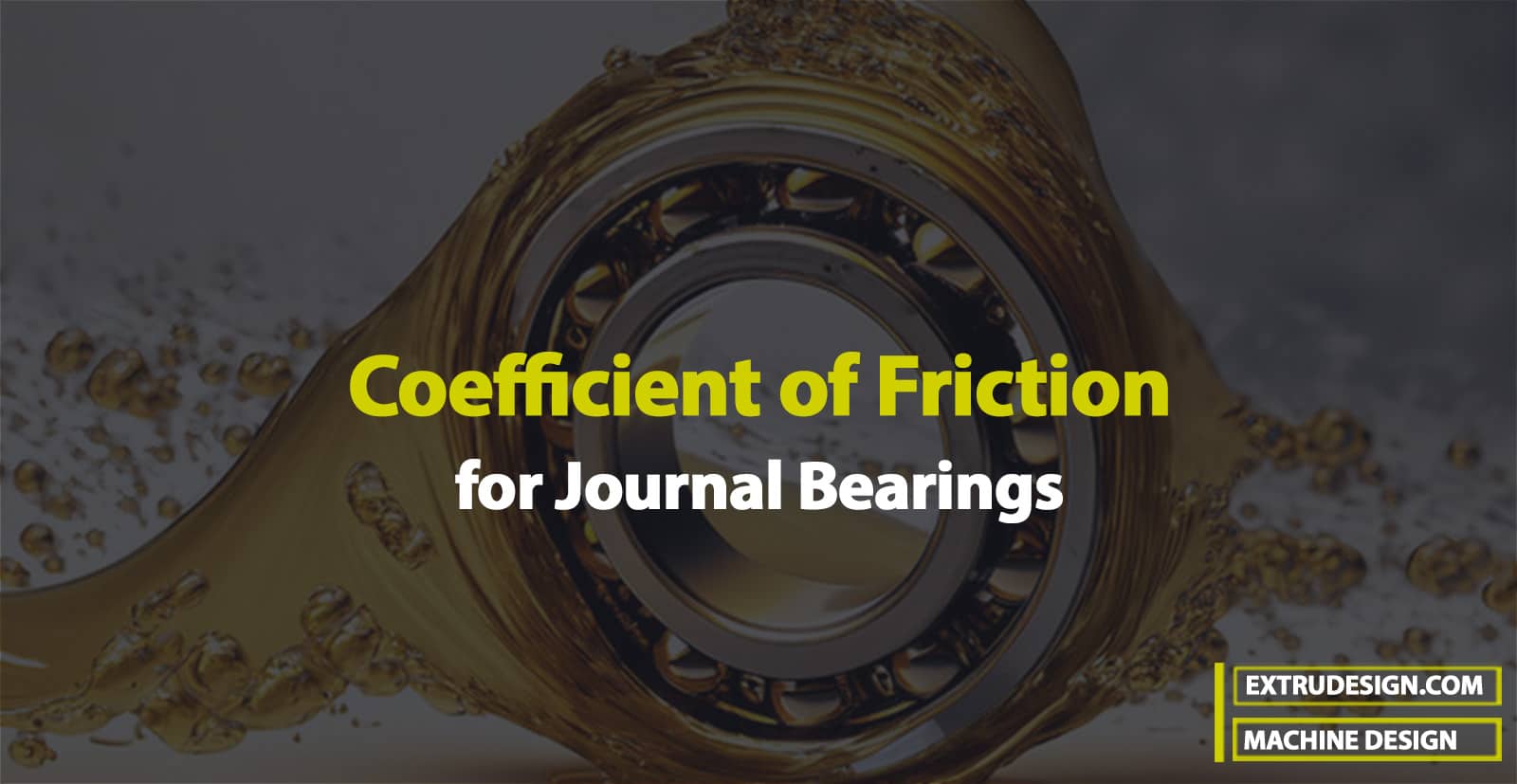
A little consideration will show that a certain amount of power is wasted in overcoming frictional resistance due to the relative motion between the contact surfaces. There will be rapid wear if the rubbing surfaces are in direct contact. To reduce frictional resistance and wear and sometimes to carry away the heat generated, a layer of fluid known as lubricant may be provided. The lubricant used to separate the journal and bearing is usually a mineral oil refined from petroleum, but vegetable oils, silicon oils, greases, etc., may be used.
Coefficient of Friction for Journal Bearings
In general, the Coefficient of Friction is defined as the ratio of the frictional force resisting the motion of two surfaces in contact to the normal force pressing the two surfaces together. It is usually symbolized by the Greek letter mu (μ)
To determine the coefficient of friction for well-lubricated full journal bearings, the following empirical relation established by McKee based on the experimental data, may be used.
Coefficient of friction,

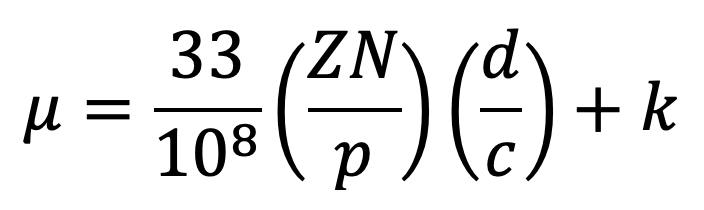
Where
ZÂ = Absolute viscosity of the lubricant, in kg / m-s
NÂ = Speed of the journal in r.p.m.,
p = Bearing pressure on the projected bearing area in N/mm2 = Load on the journal ÷ l×d
d = Diameter of the journal
c = Diametral clearance
k = Factor to correct for end leakage. It depends upon the ratio of length to the diameter of the bearing (i.e. l / d). = 0.002 for l / d ratios of 0.75 to 2.8.
The operating values of ZN / p should be compared with the values given in the following table to ensure a safe margin between operating conditions and the point of film breakdown.
Machinery | Bearing | Maximum bearing pressure ( p) in N/mm2 |
Operating values | |||
Absolute Viscosity (Z ) in kg/m-s | ZN/p (Z in kg/m-s p in N/mm2) |
c / d | l / d | |||
Automobile and aircraft engines | Main | 5.6 – 12 | 0.007 | 2.1 | – | 0.8–1.8 |
Crank pin |  10.5 – 24.5 | 0.008 | 1.4 | – | 0.7–1.4 | |
 Wrist pin |  16 – 35 | 0.008 | 1.12 | – | 1.5 – 2.2 | |
Four stroke-Gas and oil engines | Main Crank pin Wrist pin |
5 – 8.5 9.8 – 12.6 12.6 – 15.4 |
0.02 0.04 0.065Â |
2.8 1.4 0.7Â |
0.001 | 0.6 – 2 0.6 – 1.5 1.5 – 2 |
Two stroke Gas and oil engines | Main Crank pin Wrist pin |
3.5 – 5.6 7 – 10.5 8.4 – 12.6 |
0.02 0.04 0.065Â |
3.5 1.8 1.4Â |
0.001 | 0.6 – 2 0.6 – 1.5 1.5 – 2 |
Marine steam engines | Main Crank pin Wrist pin |
3.5 4.2 10.5Â |
0.03 0.04 0.05Â |
2.8 2.1 1.4Â |
0.001 | 0.7 – 1.5 0.7 – 1.2 1.2 – 1.7 |
Stationary, slow-speed steam engines | Main Crank pin Wrist pin |
2.8 10.5 12.6Â |
0.06 0.08 0.06Â |
2.8 0.84 0.7Â |
0.001 | 1–2 0.9 – 1.3 1.2 – 1.5 |
Stationary, high-speed steam engine | Main Crank pin Wrist pin |
1.75 4.2 12.6Â |
0.015 0.030 0.025Â |
3.5 0.84 0.7Â |
0.001 | 1.5 – 3 0.9-1.5 13 – 1.7 |
Reciprocating pumps and compressors | Main Crank pin Wrist pin |
1.75 4.2 7.0Â |
0.03 0.05 0.08Â |
4.2 2.8 1.4Â |
0.001 | 1 – 2.2 0.9 – 1.7 1.5 – 2.0 |
Steam locomotives | Driving axle Crank pin Wrist pin |
3.85 14 28Â |
0.10 0.04 0.03Â |
4.2 0.7 0.7Â |
0.001 | 1.6 -1.8 0.7 -1.1 0.8 – 1.3 |
Railway cars Steam turbines |
Axle Main |
3.5 0.7-2 |
0.1 0.002 – 0.016 |
7 14 |
0.001 0.001Â |
1.8 – 2 1–2 |
Generators, motors, centrifugal pumps |
Rotor | 0.7 – 1.4 | 0.025 | 28 | 0.0013 | 1–2 |
Transmission shafts | Light- fixed Self -aligning Heavy |
0.175 1.05 1.05Â |
0.025- 0.060Â | 7 2.1 2.1Â |
0.001 | 2–3 2.5 – 4 2– 3 |
Machine tools | Main | 2.1 | 0.04 | 0.14 | 0.001 | 1–4 |
Punching and shearing machines | Main Crank pin |
28 56Â |
0.1 |  — | 0.001 | 1–2 |
Rolling Mills | Main | 21 | 0.05 | 1.4 | 0.0015 | 1–1.5 |