The robust demand for custom 5-axis CNC milling parts will play a decisive role in expanding the machining industry globally. As a result, the production of complex and critical parts for industries such as aircraft, automotive, medicine, and the military-industrial complex brings good profits, and the management of machine-building enterprises will invest more in high-tech 5-axis equipment.
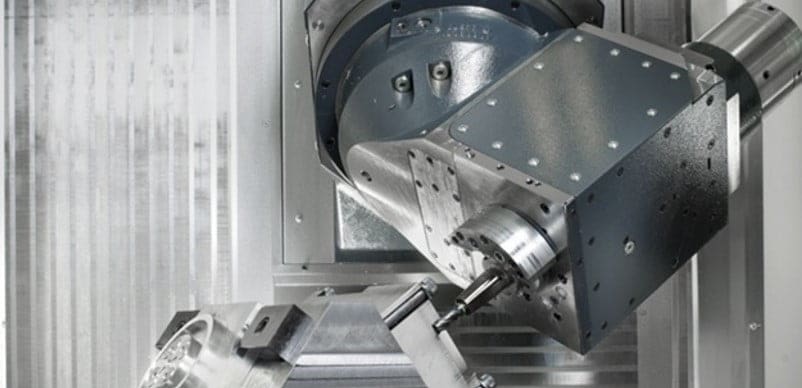
- axis tool grinding is designed with high thermal stability and process capability index. The machine’s rigid 5-axis configuration and linear motion technology ensure excellent surface finishes for 5-axis parts, even on radius and other primary reliefs, and the linear motors reduce the machine’s footprint.
In this article, we shall discuss some of the crucial design features of a five-axis tool grinder as well as in which way it has overcome traditional machining methods which can accelerate your business growth in real terms.
High-Speed Spindle
A high-speed spindle consists of several components, including the spindle housing, shaft, bearings, and motor. The spindle housing provides a rigid and stable mounting surface for the spindle and houses the bearings and other internal components.
It is a critical component in 5-axis milling that enables the cutting tool to rotate at very high speeds, up to 170,000 RPM, and its power levels should be up to 130HP. This high rotational speed is essential for achieving high-quality surface finishes, precise cuts, unique applications, and reduced cycle times in 5-axis machining.
The spindle shaft is the rotating element that supports the cutting tool and transfers the rotational energy from the motor to the cutting tool. The bearings are designed to support and reduce friction between the rotating and stationary elements, allowing for smooth operation at high speeds in 5 axis parts.
Several types of high-speed spindles include belt-driven, direct-drive, and air-driven spindles. Belt-driven spindles are the most common and are driven by a belt that connects the spindle shaft to the motor. Direct-drive spindles are connected directly to the motor and do not require a belt, providing increased efficiency and reduced vibration. Air-driven spindles use compressed air to drive the spindle shaft, providing high rotational speeds and low heat generation in 5-axis CNC machining.
Automatic Tool Changer
An Automatic Tool Changer (ATC) is a device used in 5-axis CNC grinders that automatically change tools during the custom 5-axis CNC milling process. It is designed to increase the efficiency and productivity of the grinding process by eliminating the need for manual tool changes, which can be time-consuming and error-prone.
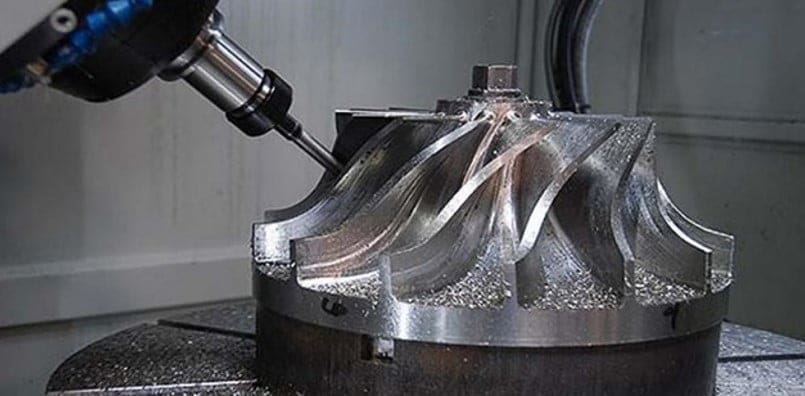
The tool arm is a robotic arm that moves the tools from the magazine to the spindle, which is attached to the machine’s spindle motor. The control system manages the entire ATC system, including tool selection, tool change sequence, and tool position monitoring.
The ATC system is integrated with the CNC machine’s controller, and the tool selection is performed through the machine’s software. The operator selects the required tool from a list of available tools, and the machine’s software communicates with the ATC system to retrieve the desired tool from the magazine. The tool arm moves the selected tool to the spindle, and the spindle motor automatically changes the tool.
The ATC system allows continuous machining without needing manual tool changes, reducing downtime and increasing productivity. The system also minimizes the risk of errors associated with manual tool changes, such as incorrect tool selection, damage to the tool or workpiece, or injury to the operator. Additionally, the ATC system increases the machine’s flexibility, allowing various tools to perform different grinding operations.
Coolant System
The purpose of a coolant system in a 5-axis CNC grinder is to provide adequate cooling while the grinding process is performed. A properly designed coolant system should be able to reduce the temperature of the grinding zone to an acceptable level and should be capable of providing cooling for long periods of time.
The design of a coolant system for a 5-axis CNC grinder must take into account several important factors. Firstly, the flow rate of the coolant must be sufficient to keep the temperature at a controlled level. The flow rate should be adjustable, as this allows the operator to adjust the cooling rate to suit the grinding conditions. Secondly, the coolant should be distributed evenly throughout the grinding area. This ensures that the temperature is kept uniform and that there are no hot spots that could cause problems.
In addition, the coolant system must be designed with safety in mind. It must be able to contain any spills and should feature shut-off valves to prevent over-pressurization. The system should also be made from materials that are resistant to wear and tear so that it lasts for a long time.
Finally, the design of the coolant system should facilitate easy maintenance and repair. This includes ensuring that all components can be easily accessed and replaced as required. Additionally, some coolant systems have built-in filtration systems to remove any particles or debris, which can cause problems with the grinding process.
Workpiece Fixturing
Design features of workpieces fixturing in 5-axis CNC grinders are essential for achieving precision and consistency in the grinding process. The proper placement of the fixture, its components, and the tools used are critical factors for obtaining maximum performance and repeatability from the machine. The primary purpose of workpiece fixturing is to provide a secure, rigid, and repeatable setup for the part being machined. This reduces vibrations during grinding, which can affect surface finish and accuracy.
There are several design features to consider when designing a fixture for a 5-axis CNC grinder including clamping and support, material selection, accuracy, adjustability, durability, and ergonomics. Clamping and support is the most important aspect of any fixture as it determines the repeatability and stability of the workpiece during grinding. It is important to select materials that will provide sufficient strength for the application and also provide a good surface finish, without compromising on accuracy.
To ensure accuracy and adjustability, clamping of the fixture should be designed for minimal deflection when loaded into a 5-axis CNC grinder. Materials used in the construction should be chosen for their ability to withstand thermal cycling, vibration, and welding processes. Consider using steels or specialty metals like Hastelloy or Inconel which are known for their strength and durability.
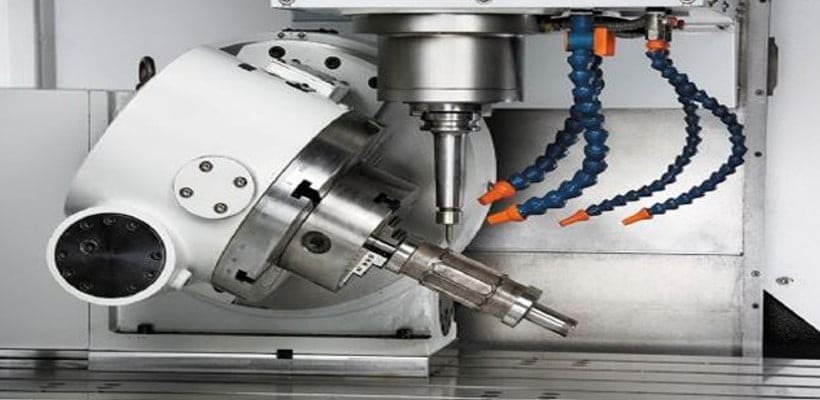
Ergonomics should also be considered when designing a fixture as this will reduce operator fatigue and help ensure safety.
Finally, the accuracy, precision, and repeatability of the part being machined are also critical for achieving maximum performance from the grinder. To this end, it is important to use the correct gaging and alignment systems for the application and to make sure the workpiece is securely held in place in order to prevent movement or distortion during grinding.
Conclusion
A five-axis tool grinder is an indispensable machine for any modern manufacturing facility. With its unique feature set and superior performance, the tool grinder offers efficient and precise cutting of a wide variety of materials.
Its advanced design features, such as its swiveling motor mount, its low-vibration direct drive spindle, and its high-precision ATC system, make it an excellent choice for any workshop. The five-axis tool grinder has become a vital tool in the machining industry, providing a one-stop solution for both large and small-scale production processes.